Volkswagen electric-car factory: the transformation of Zwickau
How VW is converting an entire car factory from internal-combustion to pure-electric production
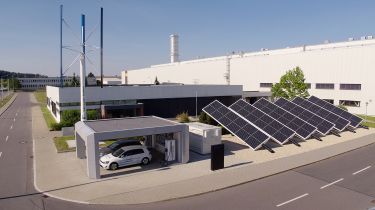
While much of the talk about infrastructure for electric cars surrounds public charging points and the capacity of the electricity grid to cope with widespread charging, equally vital is the production capacity to build enough of the cars to meet customer demand.
Germany has been an automotive production powerhouse for much of the last 100 years or so, and the Volkswagen Group is determined that it'll remain so well into the 21st century as electric cars become the norm.
As part of the group's pivot to 'e-mobility' and the development of its 'MEB' technology that'll underpin a wide range of electric cars, new plants are being constructed and old ones converted at several locations around the world as production of the new Volkswagen ID.3 hatchback looms.
DrivingElectric recently visited one such plant in Zwickau, in the state of Saxony in eastern Germany. Once a site of Trabant production in the Communist era (below), as well as the home of the Audi and Horch brands even earlier, in more recent years this 1.4-million-square-metre factory has been churning out in the region of 300,000 Golf hatchbacks and estates per annum.
But in mid-2016, the decision was taken to make this plant the 'nucleus' for production of cars on the MEB platform. According to Thomas Ulbrich, member of the Volkswagen board for e-mobility, the Zwickau project is "the largest and most difficult plant transformation" the company will undertake.
"There will be a big complete ramp up in production over the next five to 15 years with [electric] cars," Ulbrich told us. "Some plants will be completely transformed, one will be split 50:50 between internal-combustion and electric cars, and in China we are building one completely new plant for electric cars."
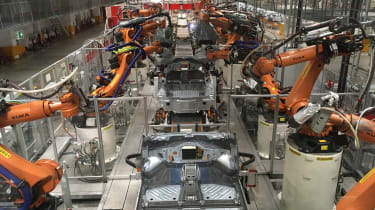
Other locations in Germany that will contribute to Volkswagen's electric-car manufacturing capacity include Emden, Hanover and Dresden. Volkswagen Group electric vehicles will also be produced by the Skoda factory in Mlada Boleslav, in Chattanooga in the United States and in Anting and Foshan in China.
The work to convert Zwickau has included the construction of 12 entirely new buildings, as well as the extension of the existing press shop. Five of the buildings have already been constructed, with seven more nearing completion; 3,500 tonnes of steel and 12,200 cubic metres of concrete are being used. VW's total investment in the location runs to €1.2 billion, with in the region of €800 million already spent.
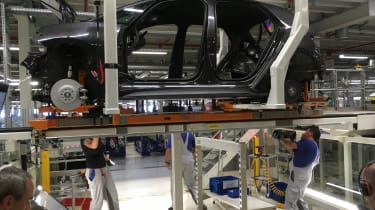
There are two production lines at Zwickau, each made up of a body shop, paint shop and assembly area; the first is being converted in time for ID.3 production to begin in November, the second will be converted during 2020 in readiness for the factory going 100% electric by 2021. A total of 1,600 new robots have been installed as part of the revamp, and production of the current Golf is continuing on the second line as the first is being converted, with no interruption in output.
Ulbrich estimates the electric-car production line will be in the region of 15 to 20% more efficient than the internal-combustion line it's replacing. Amid talk of efficiency, however, there will not be large-scale job losses at the site as a result of the shift to electric.
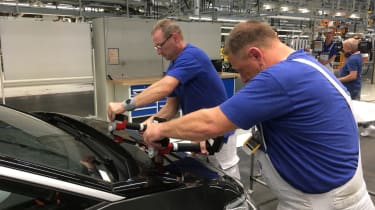
"With the transformation of the plant, we are increasing capacity and the content of the work to cover the employment we have today, with the exception of a small reduction in headcount that will be covered by retirements," said Ulbrich.
The majority of the current almost 8,000-strong workforce are being retrained to work on an electric-car production line, including some of them gaining qualifications for working with high-voltage electrical systems. By the end of August 2019, 3,800 employees had completed this training in the course of 8,000 training days, with another 13,000 training days still to be delivered.
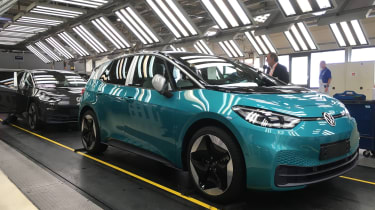
CO2 emissions reduction has been a key focus as Volkswagen develops its electric cars, and the brand is promising the ID models will be "carbon-neutral at the point of handover" to the customer. Zwickau runs on renewable energy (hydroelectricity) and VW has required its key suppliers to do the same. A small amount of unavoidable CO2 produced during the production process has been offset with the purchase of carbon credits.
Full production of the ID.3 is set to begin at Zwickau in November, but VW has already made around 2,000 pre-production ID.3s on the line, which will be used for a variety of tasks, including crash tests and final hot and cold-weather testing in locations including South Africa and Finland.
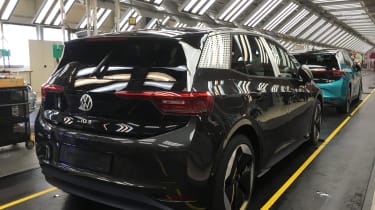
Once ID.3 production begins, it will be gradually ramped up as Golf production in the factory is wound down. By 2021, the factory will have shifted entirely to ID.3 production, churning out 330,000 cars a year – 150 more each day than before, or one every 90 seconds.
Recommended

Polo-sized electric Volkswagen ID.2 spotted testing in Germany
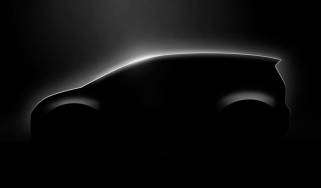
Volkswagen targets £17k city car, but you’ll have to wait until 2027
Most Popular
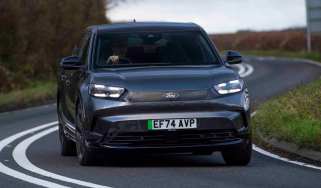
EV Deal of the Day: budget-friendly Ford Capri for just £234 a month